The
Roper Solar Greenhouse
215 Maywood Street, Blacksburg, Virginia (37° 16'3.42"N 80° 24'46.24"W)
Located in the Hale-YMCA Community Gardens (Map)
Roper Solar Greenhouse Features
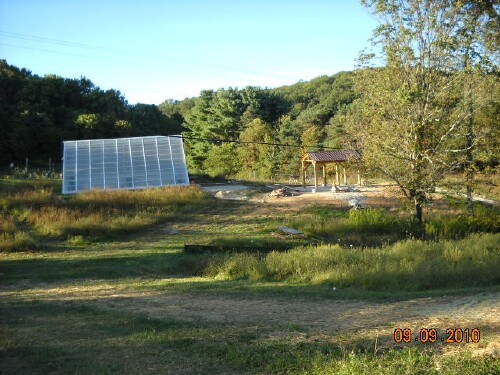
Regularly redisplay this web page to keep up on the progress of the YMCA Solar Greenhouse.
Official ground breaking for the YMCA Solar Greenhouse
Slide Show about the YMCA Solar Greenhouse
Handout about the YMCA Solar Greenhouse
Roanoke Times article about the YMCA Solar Greenhouse
Roanoke Times blog about the YMCA Solar Greenhouse
YMCA Solar Greenhouse in Solaripedia
YMCA Solar Greenhouse article in the Current Real Estate section of The Roanoke Times 11 April 2009
The YSGH was on the 2009 NRV Green Building Tour 25 April 2009
Anderson & Associates Newsletter
Roanoke Times Article about the opening of the Roper Solar Greenhouse
Video about Roper Solar Greenhouse
Blog about Arlean Hale Lambert establishing the Hale-YMCA Community Gardens
A garden set to produce for generations to come
There was a public naming and opening of the YMCA Solar Greenhouse at 10:00 AM on Thursday 15 October.
Example of a backyard solar greenhouse using the SHCS
Contents
What is a Solar Greenhouse?
Many people think that any greenhouse is a solar greenhouse. That is not correct. A solar greenhouse has the ability to store much more energy from the Sun than does an ordinary greenhouse. The energy is usually stored in water or rocks inside the greenhouse, taking up floor space. See Solar Greenhouses for more information.
A solar greenhouse (SGH) differs from a standard greenhouse in that energy is collected from the Sun and stored for use when the Sun is not shining. Greenhouses tend to get too hot when the Sun is shining and too cold during winter nights. A SGH stores energy in some medium other than the air and the soil during sunny weather. The best SGH cools the air as needed when the Sun is shining as well as heats the air when needed. This process of cooling and heating needs to be done with a minimum of energy input from external sources other than the Sun.
The YMCA Solar Greenhouse uses a new way to store energy collected from the Sun, in a subterranean heat sink of soil/rocks/water under the planting beds. This system is called the Subterranean Heating and Cooling System (SHCS).
Why Build a Solar Greenhouse?
Global Warming and Peak Oil require that humans acquire their food from local farmers or grow it themselves. In climates with cold winters, such as at Blacksburg, Virginia where Virginia Tech is located, acquiring local food in the winter time requires the existence of solar greenhouses. Of course, one could preserve summer crops by canning and drying, but fresh vegetables in winter months would make a healthy diet more likely.
The YMCA at Virginia Tech Community Gardens
The YMCA at Virginia Tech has managed a community-gardens area on property of the Town of Blacksburg for several years. A 15-acres area at the end of Maywood Street (215 Maywood Street) off of North Main Street in Blacksburg is being developed into a larger YMCA-at-Virginia-Tech Community Gardens. It is called the Hale-YMCA Community Gardens. It has been beautifully designed by Anderson and Associates:
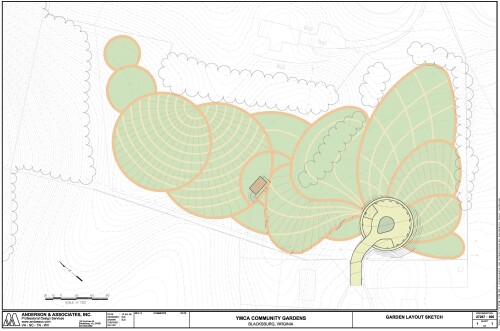
The parking lot and the curved path from the parking lot to the YMCA Solar Greenhouse will be built by UXB International using the KimsRoads technique.
The YMCA at Virginia Tech Solar Greenhouse
An 18'x32' SGH utilizing the Subterranean Heating and Cooling System (SHCS) has ben built as part of the Hale-YMCA Community Gardens. As far as is known, this will be the first large SGH using the SHCS in the United States east of the Mississippi. It is called the YMCA Solar Greenhouse (YMCA SGH or YSGH).
A model of the YMCA SGH, made by Dave Nickerson, is in a display case inside the front door of the YMCA Center at 1000 North Main Street in Blacksburg VA.
YMCA SGH Steering Committee consists of Pat Bixler (chair), Tim Colley (architect), Gail Billingsley (YMCA of VT), Arlean Lambert (land owner), Justin Boyle & Jason Boyle (Green Valley Builders, Inc.) & Dave Roper.
The site plan was made by Anderson & Associates. The design of the YSGH was made by L. David Roper. The architectural drawings were made by Colley Architects. Engineering calculations were done by Truesdell Engineering. The construction is being managed by Green Valley Builders, Inc.
Several businesses have donated time and materials to build the YMCA solar greenhouse.
Back to the top
Some Details about the YMCA Solar Greenhouse
Location
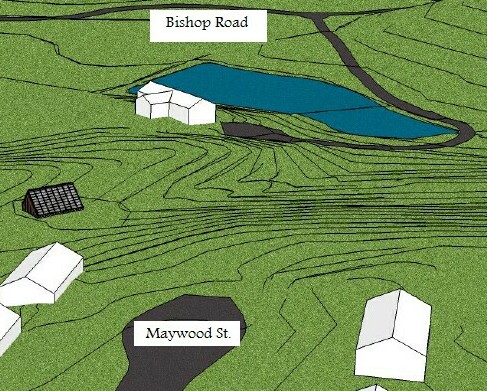
The best orientation is with the glazing toward geographical south. In Blacksburg VA magnetic north is about 6.5 degrees west of geographic north, so magnetic south is about 6.5 degrees east of geographic south.
Computer Model
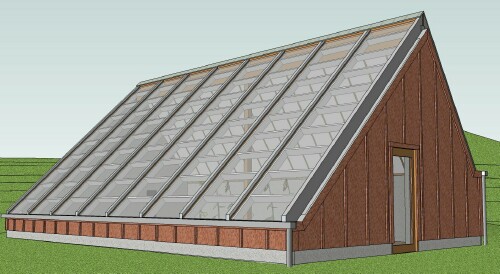
Not shown are two 2'x2' vent Marvin awning windows high on the east and west ends. They are opened and closed electrically controlled by a thermostat. There is a fan on the west window, controlled by a thermostat, to push air out that is pulled in the east window and the door, if it is open. |
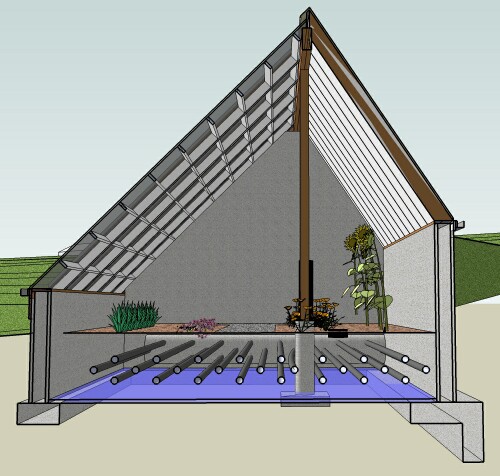
The south 45 ° roof is 10-mm thick double walled polycarbonate; the north 60° 10"-thick roof is insulated.
|
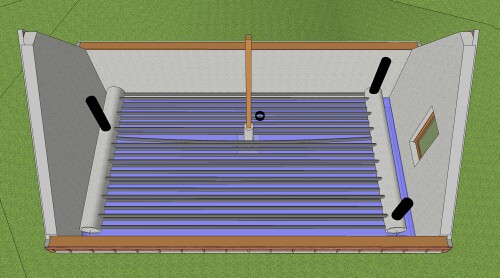 |
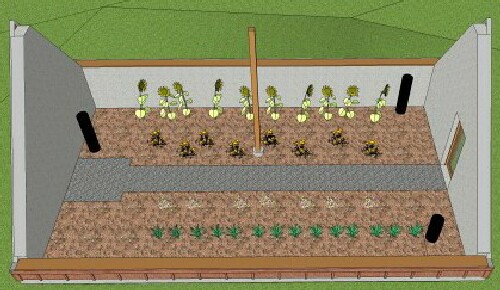
The rows should be planted north-south instead of east-west as shown here, in order to get more equal sunlight on the plants. |
The computer model was made by Tim Colley and Travis Rookstool of Colley Architects PC. Anyone wishing to obtain detailed plans for this SGH or a revision for a different size of SGH should contact Colley Architects.
Dave Nickerson made a physical model, which is on display in the YMCA Center at 1000 North Main Street in Blacksburg VA.
Back to the top
End Vent Windows
Marvin Infinity Awning Window:
"One word describes Infinity® from Marvin Casements and Awnings -- easy. They are easy to choose, easy to operate and easy to love.The Casement (left or right hinged) and Awning (top hinged) combine beauty and virtually an effortless operation. The standard Easy Wash® hinge is just that--a design that lets you easily clean the window both inside and out. The optional Clear View® hinge provides for an optimal viewing area. Both Casements and Awnings feature folding handles that tuck conveniently out of the way of most window treatments and provide a clean, finished look." The windows used are 2'x2'.
Thermostatically controlled vent-window opener:
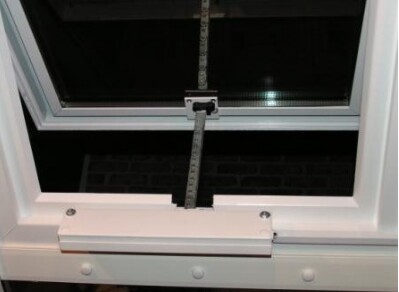
It will be opened (at 90° F) and off (at 70° F ) by a thermostat. |
|
Fan for the east vent window:
It will be turned on (at 95° F ) and off (at 75° F ) by a thermostat.
It is 170/145/115 watts and 3560/3120/2510 cfm for fast/medium/slow speed.
Two of these fans failed, probably due to the hot summer temperatures (up to 140° F!).
The replacement fan is:
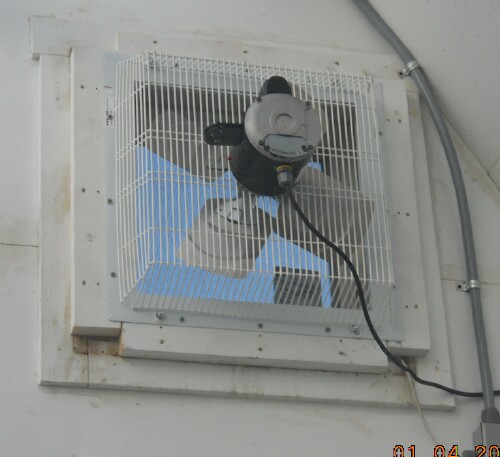
It came with fins on the outside, which were removed.
It pushes 3000 cfm.
|
Back to the top
LED/Fluorescent Lights
Three of the light bulbs will be 9.6-watts (300 lumens) LEDs (cool: 6000K; warm: 3000K; GrowLED: 5-watts, 300 lumens, 130 red, 30 blue), others will be compact fluorescent bulbs (CFL). They will cut down greatly the use of electricity for lighting and on the problem of replacing bulbs in the six ceiling lights.
Walls
The below-ground walls are made from ICF (Insulated Concrete Form) filled with concrete. The R value is 32 (ft²·°F·hour/Btu). The above ground walls are 2"x6" wood studs on 2' centers filled with 3" of closed-cell foam insulation. The inside and outside finish is a fiber-cement panel (HardiePanel).
Roofs
The north roof is 2"x10" wood rafters on 2' centers filled with 3" of closed-cell foam insulation; its inside finish is a fiber-cement panel (HardiePanel) and the outside finish is architectural shingles. The south roof is 10-mm x 4' x 20' double-walled polycarbonate on 4"x10" rafters on 4'3/4"-4'1" centers purchased from Sundance Supply. The polycarbonate sheets are attached to the rafters using the Base and Cap system.
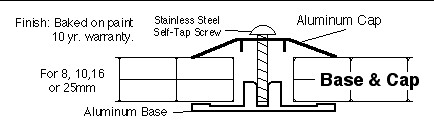
The rafters connect at the top to a 34' long 4"x14" beam.
Nine polycarbonate panels (20' long):
Back to the top
Ground Water Exclusion
All ground water must be excluded from entering the heat sink. This is done by the following systems:
- The ICF walls have a water-barrier film on both sides that are underground; the inner-side film is to prevent the insulation there from getting wet from the water in the heat sink.
- The 2" insulation board under the heat sink has a water-barrier film on both sides; the upper-side film is to prevent the insulation from getting wet from the water in the heat sink. The top film should be a thick plastic to keep the rocks on top of it from puncturing it.
- A drain pipe goes around the outside of the wall to carry water away from the SGH.
- A water-barrier film slopes 10' away from the soil surface at all four walls walls to carry water away from the SGH. (May not be necessary because of berming on the high hill side and sloping away on the low hill side.)
- Drain troughs on both sides of the roof carry rain water to an underground 1500-gallon cistern on the south side of the southeast corner of the SGH.
Ceiling Fans
Two 36" Action-Aire ceiling fans, actuated by a switch and a Ranco adjustable digital thermostat will be hung from the SGH peak centered between the center post and the two walls. Their purpose is to keep hot air from accumulating at the peak.
The thermostat sensor will be placed near the peak, shielded from sunlight. It will be set to turn on at 90° F and off at 70° F. The thermostat could be in the same box as the thermostats for the heat-sink fan, with a long lead to the sensor near the top.
The switch for the ceiling fans could be in the same box as the thermostats, out of range of prying eyes.
Electrical Details
Here are some considerations for the electrical wiring of the YSGH:
- Some of the light bulbs will be LEDs, others will be compact fluorescent bulbs. They will cut down greatly the use of electricity for lighting and on the problem of replacing bulbs in the eight ceiling lights.
- The heat-sink fan’s two parallel thermostats and their sensors need to be inside a box on the west wall out of the sunlight and prying eyes. It is maximum 241 watts.
- The sensor for the thermostat for the exhaust fan in the west vent window needs to be out of sunlight near the top of the SGH. The thermostat could be in the same box as the thermostats for the heat-sink fan, with a long lead to the sensor near the top. It is maximum 170 watts.
- The switches for the interior and exterior lights should be near the door. The switches for the heat sink and ceiling fans could be in the same box as the thermostats, out of range of prying eyes.
- The switch for the water pump should be on the center post near the water pressure tank.
- Eventually there will be a battery-backup system for the heat-sink fan, and possibly other electrical components, to keep the YSGH temperature and humidity at appropriate values during times when the grid power is off.
The estimated power usage is 425 watts for the fans, 400 watts for the water pump and 300 watts for the lighting. The total is about 1125 watts.
Planting Beds
Here are results of the top-soil tests for the SGH site:
Analysis: |
P (lb/A) |
K (lb/A) |
Ca (lb/A) |
Mg (lb/A) |
Zn (ppm) |
Mn (ppm) |
Cu (ppm) |
Fe (ppm) |
B (ppm) |
Soluble
Salts |
Result: |
7 |
46 |
1150 |
149 |
0.7 |
4.3 |
0.4 |
5.2 |
0.3 |
1 |
Rating |
L |
L |
M |
H- |
Suff |
Suff |
Suff |
Suff |
Suff |
L |
|
|
|
|
|
|
|
|
|
|
|
Analysis: |
Soil pH |
Buffer Index |
Est.-CEC (meq/100g) |
Acidity (%) |
Base Sat. (%) |
Ca Sat. (%) |
Mg Sat. (%) |
K Sat. (%) |
Organic Matter (%) |
|
Result: |
6.2 |
6.34 |
3.9 |
9.2 |
90.9 |
73.6 |
15.7 |
1.5 |
2.8 |
|
lb/A = lbs per acre; Sat. = saturation; Est-CEC = estimated cation exchange capacity; g = gram, Suff = sufficient; ppm = parts per million; L = low; M = medium, H = high, meq = millequivalent
Lime recommendations: Apply 2 lbs of agricultural limestone (ground or pulverized) per 100 sq ft.
|
|
Fertilizer recommendations: Apply 4 lbs of 5-10-10 per 100 sq ft. |
|
|
|
|
Soluble salts are not high enough to cause salt injury.
|
|
|
|
|
|
The National Sustainable Agriculture Information Service may be of help in preparing the SGH soil for planting:
Hydrologic Soil Group Descriptions:
- A -- Well-drained sand and gravel; high permeability.
- B -- Moderate to well-drained; moderately fine to moderately coarse texture; moderate permeability.
- C -- Poor to moderately well-drained; moderately fine to fine texture; slow permeability.
- D -- Poorly drained, clay soils with high swelling potential, permanent high water table, claypan, or shallow soils over nearly impervious layer(s).
A planters' committee (Abigail Convery, John Ogburn, Deborah Wiley and Holly Scoggins) are studying what to use for topsoil; e.g., whether it will involve the original topsoil or not. One option is growing mixes by SunGro.
Sun Gro donated 75 bales of Organic #1 Mix in 3.8 ft3 bales (which expands to 7 ft3 for a total of 525 ft3 [~19.5 yd3]). This will be mixed with builders sand (10% or 2.8 yd3) and worm castings or top soil (20% or 5.6 yd3) to make the approximately 28 yd 3 needed for the planting beds. McEnroe Premium Organic Compost was used and a few bags of Azomite were added.
Back to the top
Walkway
Under the 3'-wide walkway and the 5'x5' turn-around at the west end will be #57 stone (~8.5 tons) from the tarpaulin at the top of the heat sink up to about two inches below the top of the planting bed. It will be installed at the same time as the planting soil is added to the two planting beds on each side of the walkway. On top of the rocks will be a walkway made of 5/4"x6" Trex "boards" with Trex ribs under them to hold them together. (Eight 16' Trex boards.)
Building the walkway:
- Lay down the punctured tarp pieces on both sides of the walkway.
- Lay a slotted 4" pipe in the bottom of the walkway, connected to the two 24" pipes at each end.
- Build the walkway with Hardie board sides and rocks on the inside.
- Lay the not-puntured tarp piece on the walkway and down both sides of it, to drain water into the flower beds instead of into the rocks underneath..
- Haul in the soil parts and mix them.
- Build the Trex walkway
Cistern for Storing Rain Water for the Plants and Watering
A 2000-gallons concrete septic tankwith their tops 2' below ground on the south side of the southeast corner of the SGH will store rain water that falls on the roof to be used for watering the plants. There will be filters to keep debris from entering the cistern. At the beginning town water will be hauled in to mostly fill the cisterns.
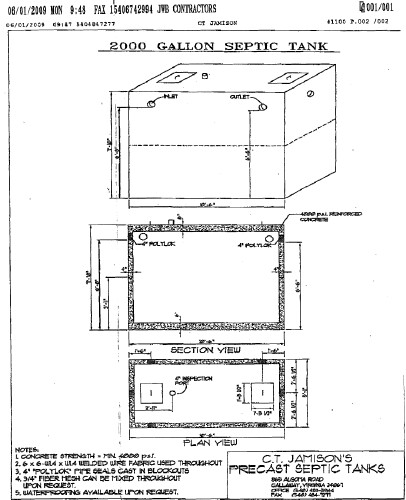
The water will be pumped out of the cisterns by a Commander pump into a pressure tank behind the center post of the SGH.
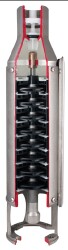
There are two water faucets, one at each end of the walkway.
Instrumentation
-
Two
Onset HOBO U10-003 temperature and humidity data sensors/loggers and
HOBOLite software donated. One will be place at the heat-sink air inlet and the other will be placed at one of the two heat-sink air outlets:
-
-
Onset HOBO U12-012 temperature, humidity and light-intensity data sensors/logger donated. This will be placed behind the center post:
-
.
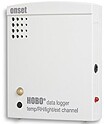
-
-
.
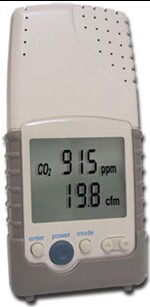
-
AM-4220 anemometer for measuring air flow out of heat-sink outlets donated. This will be used at one of the two heat-sink air outlets to determine the air flow:
-
-
-
.
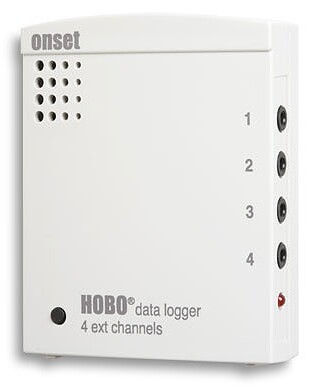
See some data collected using the data loggers.
Start-up Procedure for a SGH using Subterranean Heating and Cooling System (SHCS)
The problem is that some water and heat needs to be stored in the heat sink below the planting bed before vegetable greens are planted in the SGH. In normal operation that water and heat comes from the 90% transpiration of water from plant leaves that comes from watering the plants in the soil. So, it is a “chicken and egg” quandary.
Here is a possible procedure to solve the quandary: After water is hauled in to mostly fill the cistern at the start, some of that water is sprayed into the SGH air and placed in pans on several consecutive sunny days, so that the SHCS can start to work by pulling humid air into the heat sink. Then watch the temperature and humidity for some cold days to see if the heat sink is working. Some lettuce starts will be quickly planted.
Also, the heat-sink fan's rheostat needs to be adjusted for the correct air flow in the heat-sink pipes. The HOBO U10-003 temperature and humidity data sensors/loggers at the heat-sink inlet and outlet pipes will be used to determine the correct air flow to yield the biggest difference in temperature and humidity at those two locations on sunny days.
After a week or two of testing, hopefully confidence will be built so that plants can be planted.
Soil heating cables may be used to get plants started.
Back to the top
Time Table and Volunteers
- Late 2006 & early 2007: L. David Roper began collecting information about solar greenhouses (SGH), hoping to eventually build some in Blacksburg VA in order to grow food in the winter time. A web page containing the information was created. He roughly sketched a neighborhood solar greenhouse and a backyard solar greenhouse.
- July 2007: Discussions were initiated between Pat Bixler and Dave Roper about building a SGH using the Subterranian Heating and Cooling System (SHCS) in Blacksburg VA.
- August 2007: Discussions were initiated with Gail Billingsley about the YMCA of VT building a SGH.
- September 2007: Discussions were initiated by Dave Roper with Tim Colley, architect, about doing the architectural drawings for a SGH. Tim agreed and was joined in the effort by Travis Rookstool.
- January 2008: A small-scale model of a neighborhood SGH was made by Dave Nickerson, with slight assistance from Dave Roper. Several changes were made in the design after the model was made.
- February 2008: First meeting of SGH Interest Group was held. (Contact Dave Roper, roperld@vt.edu, to add your name to the e-mail list)
- 17 April 2008: First meeting of YMCA SGH Steering Committee was held.
- April 2008: Discussions were initiated by the YMCA with Anderson & Associates about doing the site planning for the YMCA SGH. They agreed and several meetings were later held to discuss the evolving site plan. Steve Somick did the design.
- May 2008: Discussions were initiated by Dave Roper with Prof. Naraine Persaud in the Virginia Tech Dept. of Crop & Soil Environmental Sciences about the science of the SGH heat sink soil and the instrumentation of the SGH. Several more meetings were later held to discuss the evolving plans for instrumentation.
- May 2008: Prof. Persaud wrote a proposal for a Virginia Dept. of Agriculture Consumer Services (VDACS) grant for ~$16,000 for instrumentation for the YSGH.
- May 2008: Discussions were initiated by Pat Bixler with Green Valley Builders, Inc. to manage the construction of the YMCA SGH. The owner's, Jason & Justin Boyle, agreed.
- 11 July 2008: Architects' drawings and site plan were submitted for approval to Town of Blacksburg.
- 28 July 2008: Building permit was approved by the Town of Blacksburg.
- 30 July 2008: The $15,979 grant for the instrumentation of the YSGH was approved by the VDACS.
- 30 July 2008: Started planning with Abigail Convery of the YMCA of VT for first plantings in the YSGH.
- 3 August 2008: Funding hold was put on VDACS grant because of state of Virginia budget shortfall.
- 23 October 2008: Excavation was started by J. W. B. Contractors (Jeff Buchinsky)
- 24 October 2008: Footer concrete was installed.
- 1 November 2008: Prof. Naraine Persaud gathered together instruments for the YSGH.
- 5 November 2008: Official groundbreaking ceremony was held.
- 15 November 2008: ICF walls were installed.
- 18 November 2008: Concete from Conrock was poured by Jeff Ligon into the ICF using his pump truck.
- 20 November 2008: Soils group (Abi Convery, John Ogburn, Debbie Wiley & Prof. Holly Scoggins) started planning for top soil composition.
- 24 November 2008: Waterproofing of walls was done by Snyder Waterproofing using the Tuff-N-Dri system.
- 28 November 2008: Insulation was placed at the bottom of the heat sink by Justin Boyle, Jason Boyle, Pat Bixler, Devon Bixler, Dave Roper, Brian Kenny, Craig McNally, Josh Hanna and Jason Pall. Also, some of the first 4" layer of rocks was put in place.
- 4 December 2008: Backfill was started.
- 5 December 2008: Built the 3'-deep heat sink, installed framing base and painted rafters and the beam with the help of Justin Boyle, Dave Roper, Pat Bixler, Alex Lawrence, John Ohanian, Philip Schucharde, Etan Karne, Michael Armstrong, Michael Link, Andy Zoko, Laura Collins, Scott Helsing, Josh Hanna, Lynado Guerroro, Bill Sisk (photography), Jennifer Chang (painting), Chris Olien, Adam Lasley, Matt Nottingham, Jason Pall, Richard Reid (framing), Tom Bowden (framing), Gina Davis (painting) and Beth Lohman (painting). Special thanks go to Alex Lawrence, Jason Pall, Chris Roberts (Baseline Solar Solutions, electrical & heat sink), Josh Hanna and Dave Roper for staying to the end of building the heat sink. Pizza for lunch was supplied by Pat Bixler. Some of these people are employees of AVID LLC.
- 8 December 2008: Chris Roberts & Pat Bixler (Baseline Solar Solutions) & Dave Roper covered the YSGH with a large tarp to keep predicted rain out until the framing is done.
- ? December 2008: Several community service workers painted on the rafters and blocking boards.
- 11 December: David Bernard (Aquarius Plumbing) had a crew pump rain water off of the tarp covering the heat sink. Later wind blew the tarp off.
- 13 December 2008: Pat Bixler and Dave Roper put the tarp back on as a liner inside the heat sink to catch the rain water predicted for the next week.
- 20 December 2008: Dave Roper put 1/4" wire screen over the inlet and outlet pipes.
- 21 December 2008: Chris Roberts (Baseline Solar Solutions) started the electrical wiring.
- 26 December 2008: Dave Nickerson, Jim Mitchell & Dave Roper painted on the 34'x4"x14" beam.
- 1 January 2009: Pat Bixler & Dave Roper finished painting the beam.
- 3 January 2009: Rafters and beam were cut by Richard Reid, Jason Boyle & Justin Boyle. Dave Roper tossed chunks of ice from off of the tarp covering the heat sink.
- 5 January 2009: Abigail Convery & Dave Roper finished painting the large rafters, except for touch-up that will be needed after the framing is completed.
- 8 & 9 January 2009: Dave Roper tossed chunks of ice from off the tarp covering the heat sink.
- 9 January 2009: Justin Boyle, Alex Lawrence and Hammer Down Construction (John Sullivan, owner; Jason Quesenberry; Rusty Hazen) started building the roof.
- 10 January 2009: Justin Boyle, John Sullivan, Dave Roper, Josh Hanna, Richard Reid, Tom Bowden, Alex Lawrence and Tim Colley finished placing the rafters, installed the temporary north roof and installed the south-roof blocking between the rafters. Pizza for lunch was supplied by Dave Roper.
- 12 January 2009: Dave Roper painted the top board above the beam.
- 13 January 2009: Dave Roper put lag bolts in the bottom of the inlet and outlet pipes to hold them in place.
- 20 January 2009: Alex Lawrence (Green Valley Builders) and Hammer Down Construction (John Sullivan, owner; Jason Quesenberry) finished installing the south-roof blocking between the rafters, installed the center post and framed the west end.
- 22 January 2009: Several community service workers moved the polycarbonate from the entrance to the gardens to the YSGH site.
- 24 January 2009: Framed the east end (which finished the framing), installed the base metal holders for the polycarbonate, put in the two vent windows and dug out around the walls with the help of Jason Boyle, John Sullivan, Pat Bixler, Dave Roper, Sandy Knapp, Alex Kassir, Susan Mattingly, Kelly Mattingly, Richard Reid, Arslan Khan, Steve Boyle, John Spicer, Tim Colley and Tom Bowden.
- 26 January 2009: Abigail Convery & Dave Roper put a primer coat on the bottom board of the south roof and an east-end board.
- 29 January 2009: Dave Roper put the finish coat of paint on the bottom board of the south roof and an east-end board.
- 3 February 2009: The Sungro soil arrived.
- 14 February 2009: The polycarbonate was installed with the help of Justin Boyle, Jason Boyle, Steve Boyle, Pat Boyle (cookies and drinks), Dave Roper, Pat Bixler & Chris Roberts (Baseline Solar Solutions), Richard Reid, Tim Colley, Jeffrey Wiseman, Gail Billingsley (pizza and drinks).
- 20 February 2009: Abigail Convery and Hiwote Getaneh put up temporary plastic sheets to protect the polycarbonate when the insulation is blown in between the north-roof rafters and the side studs.
- 25 February 2009: Snyder & Associates finished water proofing the walls.
- 28 February 2009: Laura Doody and the Sigma Delta business fraternity move the Sungro packet from the entrance to nearer the SGH.
- 21 March 2009: Travis Radford and Daniel Weber of Evergreen Insulation, assisted by Justin Boyle, sprayed closed-cell foam into the north ceiling and the two end walls. Abi Convery & Dave Roper moved the remaining Sun Gro bales from the gardens entrance to near the SGH.
- 24 March 2009: Evergreen Insulation scraped the insulation off of the rafters' and studs' edges.
- 25 March 2009: Volunteers Laura Doody, Bo Ram Kim, Carolyn Bea & Tyler Nichols cleaned up, painted Hardie boards and patched cracks with Abigail Convery (YMCA).
- 2 April 2009: The German Club Pledge Class of 2009 painted some of the Hardie boards.
- 5 April 2009: The Virginia Tech Air Force ROTC (Brandon Cho, Daniel Collins, Ryan Meritt, Josiah Donaldson, Alisha Temples, Sansen Johnson and Joshuah Hess) cleanup up site and painted 4'x8' Hardie boards. Gail Billingsley and Dave Roper helped.
- 6 April 2009: The DiStefano Siding Company started installing the Hardie board on the inside. Workers: Steven DiStefano (owner), David Bryan, Mark Hambrick & Jody St. Clair.
- 7 April 2009: The DiStefano Siding Company installed the door.
- 8 April 2009: The DiStefano Siding Company started installing the Hardie board on the outside.
- 9 April 2009: The outside siding was finished. Dave Roper painted the inside Hardie board using a long telescopic pole to reach the top.
- 10 April 2009: Dave Roper painted inside Hardie board and started wall boards for walkway.
- 11 April 2009: Chi Delta Alpha service sorority women Kelly Daly, Caron Sinnerberg & Sarah Vosti helped Dave Roper paint on the inside and they picked up trash.
- 12 April 2009: Gail Billingsley & Dave Roper did some finish-coat painting on the inside.
- 13 April 2009: Dave Roper finished the first finish inside paint coat, except for small-brush touch up.
- 14 April 2009: Dave Roper puttied cracks, seams and nail holes for 4 hours; he also prepared some of the boards for the walkway. Later Abi Convery, Ingrid Baker, Laura Doody & Meghan Green started the 2nd and final finish paint coat inside.
- 15 April 2009: Dave Roper puttied some more. Chris Roberts of Baseline Solar Solutions started installing the electical. Abi Convery, Laura Doody, Carolyn Bea & Bo Ram Kim puttied and painted.
- 16 April 2009: Dave Roper prepared boards and heat-sink pipe adaptors for the walkway, the latter with Chris Robert's help. Chris Roberts and Pat Bixler (Baseline Solar Solutions) installed the outside and inside electrical cabinets and did some wiring. Aliana Havrilla (YMCA), Charlotte Scalav, Laura Doody and Carolyn Bea started painting the primer on the outsides of the ends. Patrick Young finished some painting touch-up and puttying inside; he also helped Dave Roper prepare the tarp that goes between the heat sink and the soil andTrex boards for the top of the walkway.
- 17 April 2009: Chris Roberts (Baseline Solar Solutions) finished putting electrical conduit along the top of the heat sink. Abigail Convery had the sand delivered yesterday for mixing with the SunGro. Aliana Havrilla, Gail Billingsley and Dave Roper took the scaffolding outside. Gail Billingsley and Dave Roper started building the walkway.
- 18 April 2009: Henderson Roofing installed the shingle on the north roof. Many Y-Studend Programs volunteers helped clean up and move rocks inside. They also helped Debbie Wiley and Abi Convery mix the Sun Gro and sand for the planting beds' soil. In the evening Dave Roper and John Applequist finished constructing the boundary between the walkway rocks and the soil.
- 19 April 2009: Dave Roper hauled more rocks in for the walkway and experimented with laying Trex boards for the top of the walkway.
- 20 April 2009: Dave Roper hauled more rocks in for the walkway and cut some more Trex ribs. He ordered ten more composite boards (ChoiceDek) for the walkway.
- 21 April 2009: Dave Roper hauled more rocks in for the walkway, mixed some Sun Gro and sand and built a form for the base of the water pressure tank.
- 22 April 2009: Berek Caldwell, Carolyn Bea, Bo Ram Kim, Laura Doody, Gail Billingsley and Dave Roper hauled rocks in for the walkway and mixed the rest of the Sun Gro with sand.
- 23 April 2009: Jenny Cox, Cathlyn Cox, Laura Doody and Abigail Convery painted on the west & east ends. Berek Crawford and Laura Doody finished carrying rocks inside for the walkway. Dave Roper started installing the walkway composite boards. J. W. B. Contractors dug the hole for the cistern
- 24 April 2009: Dave Roper put all composite boards but one in place with holding screws. J. W. B. Contractors put the cistern in the ground.
- 25 April 2009: J. W. B. Contractors installed the cistern pipes and backfiledl the east and sough ends. Dave Roper finished placing all composite boards in the walkway; many more screws need to be installed. The YSGH was a site on the YMCA Green Building Tour.
- 27 April 2009: Early in the morning Dave Roper drilled holes in the walkway boards and inserted screws in them.
- 28 April 2009: Early in the morning Dave Nickerson & Dave Roper finished putting the screws in the walkway boards and poured sand in the walkway cracks.
- 29 April 2009: Dave Roper finished painting the primer coat on the west end.
- 30 April 2009: Dave Nickerson & Dave Roper finished painting the first finish coat on both ends.
- 2 May 2009: Jacob Moore & Gail Billingsley got most of the final finish coat painted. Dave Roper worked on the shelves at the west end of the walkway.
- 3 May 2009: Dave Roper attached the heat-sink fan to the inlet pipe on the west end, worked on installing shelves around the inlet pipe and attached the outlet elbows to the outlet pipes on the east end.
- 4 May 2009: Dave Roper hauled the last rocks inside to make the base for the water pressure tank. He secured the inlet pipe above the heat-sink fan.
- 5 May 2009: Dave Roper mixed the concrete for the pad for the water tank and worked on the shelving at the west end.
- 6 May 2009: Dave Roper finished sawing boards for shelves on west end and installed the ones that will not impede wiring the heat-sink fan.
- 7 May 2009: Dave Roper worked on some small items regarding the walkway and the shelves on the west end. Chris Roberts mapped out the wiring layout for the switches and thermostats.
- 8 May 2009: DiStefano Siding Company put the ridge cap on.
- 9 May 2009: Chris Roberts and Dave Roper put scaffold up for doing the electical wiring at the peak. Chris installed some conduit until the temperature got too high.
- 11 May 2009: Chris Roberts installed the electrical boxes on the east end of the peak and wired the heat-sink fan.
- 12 May 2009: Dave Roper finished putting the shelves together on the west end around the input pipe for the heat sink.
- 14 May 2009: An American Electrical Power contractor dug a trench from a power pole near the driveway to the YSGH and connected installed electrical service.
- 15 May 2009: John Ogburn donated 5 more bales of Sun Gro and mixed it with sand.
- 17 May 2009: Dave Roper finished puttying the cracks between the bottoms of the polycarbonate and the slanting boards inside.
- 18 May 2009: Chris Roberts put in a temporary electrical plug so that power tools and lights can be used inside. The water-pressure tank and cistern pump were delivered.
- 20 May 2009: Chris Roberts did some more of the wiring. Sun Gro representatives Mark Hawley & Patrick Alberti came by with Abi Convery to discuss the use of their product in the YSGH; while there they helped Chris, Abi and Dave Roper move the scaffolding so that Chris can place the lights and fan boxes on the top beam at the west end.
- 21 May 2009: David King (King & Sons Excavating) put the water-pressure tank inside and put the sump pump in the cistern.
- 22 May 2009: Dave Roper helped Chris Roberts install the electronics control box on the west wall.
- 26 May 2009: David King (King & Sons Excavating) started plumbing and wiring the cistern and its electric pump.
- 28 May 2009: Dave Roper helped Chris Roberts pull wires through conduit. Chris wired the window openers and installed a junction box for the water pump.
- 1 June 2009: Jim Lawrence and Dave Roper installed one of the two electric vent-window openers and Tickle Septic & Water delivered 1500 gallons of water to put in the cistern and 65 gallons in a small tank above the building to use to water down the Sun Gro to cut down on dust.
- 2 June 2009: Dave Roper finished installing the electric window openers.
- 3 June 2009: Dave Roper helped Chris Roberts install the west-vent-window fan. It was then left on all day to reduce the inside temperature from about 140°F to 110°F.
- 4 June 2009: Justin Boyle and David King finished the cistern connection to the water pressure tank inside. Now water is available. Gutters were installed by Blue Ridge Seamless Gutter. Dave Roper helped Chris Roberts almost finished pulling wires through the conduit.
- 5 June 2009: Dave Roper installed bug screens on the downspouts and Chris Roberts finished the rough-in wiring to enable Town of Blacksburg inspection.
- 9 June 2009: Justin Boyle put a cover on the cistern.
- 23 June 2009: Rough-in wiring inspection by Town of Blacksburg passed! Water is now running.
- 24 June 2009: Chris Roberts finished the fans and windows control box and installed the outlets.
- 25 June 2009: Chris Roberts installed the light fixtures. Superior Exterminating Company did termite treatment around the edge of the building.
- 26 June 2009: Tuna Tandogan, Gail Billingsley, John Ogburn & Dave Roper cleaned up around the building to allow the backfill to be done soon. Dave Roper recorded data that showed energy being stored in the heat sink!
- 29 June 2009: David King fixed a problem with the water system. The pump was always running, even when water was not being used.
- 7 July 2009: Backfill was done by J.W.B. Contractors.
- 9 July 2009: Dave Nickerson & Dave Roper did some finishing backfill shoveling around the edges of the building.
- 10 July 2009: Chris Roberts repaired the ground wire. Dave Roper put aluminum shielding around the connection between the gutter down spouts and the pipes to the cistern.
- 27 July 2009: Chris Roberts installed the two ceiling fans, the last electrical items to be installed!
- 3 Aug 2009: Dave Roper cleanup up construction debris and removed the ladders.
- 4 Aug 2009: Dave Roper put wing nuts to hold the cover on the control box to make it easier to remove. He also punched and drilled holes in the top and bottom of it to allow air to circulate through it to keep from holding heat inside.
- 5 Aug 2009: Dave Roper watered down the soil to settle the dust for removing the scaffold. Justin Boyle hauled most of the trash away and removed the scaffold.
- 6 Aug 2009: Dave Roper thoroughly tested the water system by thoroughly watering the Sun Gro and washing the ledges. It worked well.
- 10 Aug 2009: Dave Roper installed the screen door.
- 24 Aug 2009: Chris Roberts installed an outlet on the center post and a switch for the water pump.
- 31 Aug 2009: Hill Studio in Roanoke let a charrette about landscaping the area around the YSGH.
- 19 Sep 2009: Chris Yates, Gail Billingsley & Dave Roper finished cleaning up the construction detritus.
- 20 Sep 2009: A forestry class at Virginia Tech started building a trail from the Blacksburg New School to the YSGH.
- 22 Sep 2009: Much of the subsoil pile from the excavation was hauled away to the Blacksburg Country Club.
- 23 Sep 2009: Dave Roper put 1/4" hardware cloth on the screen door.
- 25 Sep 2009: Dave Roper watered down the SunGro and moved some of it from the west end to the east end. Abi Convery hauled the worm castings from 7-Springs Farm; Dave Roper & Alex Borgardts unloaded it into the YSGH.
- 30 Sep 2009: Abi Convery hauled the compost from 7-Springs Farm.
- 1 Oct 2009: Abi Convery & John Ogburn & others mixed the soil. Dave Roper gave a talk to the Mt. Tabor Ruritans about the YSGH.
- ~7 Oct 2009: The middle students at Blacksburg New School started planting in the west half and John Ogburn and his gardening group started planting in the east half.
- 16 Oct 2009: Grading by C. R. Sult began for the parking lot.
- 21 Oct 2009: The KimsRoad hard surface for the parking lot installation was started.
- 22 Oct 2009: Dave Roper installed temperature probes in the heat sink and the soil.
- 27 Oct 2009: Dave Roper & John Ogburn installed a 200-gallons water tank behind the center post and against the wall.
- 2 Nov 2009: Dave Roper filled the 200-gallons water tank with water.
- 16 Nov 2009: The west ceiling fan quit. Chris Roberts removed it.
- 17 Nov 2009: Chris Roberts installed a timer on the water pump switch.
- 29 Nov 2009: Dave Roper shaved some woof off of the screen door to make it shut better.
- 1 Dec 2009: Dave Roper ordered 1500 ladybugs to eat the aphids that are in the RSGH.
- 3 Dec 2009: Dave Roper installed a plastic front cover on the control box, so that the insides can be seen.
- 5 Dec 2009: Dave Roper released ~1500 ladybugs inside to help control plant-damaging pests such as aphids.
- 6 Dec 2009: Chris Roberts installed a replacement ceiling fan on the west end.
- 11 Dec 2009: Chris Roberts worked on fixing a bad thermostat for opening/closing the vent windows. They had been staying open during teens nightly temperatures with forties temperatures inside. Joe Mugavero of Energy Check did a blower-door test: Fractional air changes per hour was 0.06, which is very good. The infrared camera found some spots that could use fixing.
- 10 Mar 2010: Dave Roper installed a Schlage combination dead-bolt lock on the door.
- 10 Jun 2010: Heritage Stone Productions installed a rock patio outside the RSGH door.
- 26 Aug 2010: Virginia Gutters installed K-Guard gutters with a hood to keep out trash.
- 8 Sep 2010: Heritage Stone Productions installed rock walls around the rock patio.
- 10-11 Oct 2010: Dave Roper installed Suncast QE20 EcoEdge between each 4'x7' plot.
- 12 Feb 2011: Chris Roberts & Patrick Feucht (Baseline Solar) installed a Davis Instruments Vantage Vue weather station above the west end.
- 16 Feb 2011: Chris Roberts installed a replacement window fan.
- 10 May 2011: Naraine Persaud, John Gordon and David Roper started building a locked cage for instrumentation.
- 11 May 2011: David Roper painted the instrument cage.
- 16 May 2011: Naraine Persaud and David Roper finished building and installed the instrument cage.
- 20 May 2011: David Roper painted the door of the instrument cage.
- 21 May 2011: David Roper installed the cable modem, router and weather-station display in the instrument cage.
- 1 Sept 2011: Naraine Persaud installed a computer in an outside box.
- 17 Sep 2011: Aquarius Plumbing replumbed the inside water pipes to move them from obstructing the planting beds.
- Sep 2011: Jeffrey Glesner and David Roper laid out the location of the stairs up to the RSGH; two days.
- Oct 2011: Richard Reid built 2'-wide screen-bottomed shelves 4' above the soil on the north wall to give more growing area and repaired the screen door.
- 10 Oct 2011: Randy Sult of C. R. Sult Excavating sloped the dirt in front to allow snow to slide off of the polycarbonate and created a terrace in front of the slope.
- Oct 2011: David Roper numbered the 16 plots and put name plates on the walkway for them.
- Nov 2011: Blacksburg Rotary Club built steps from the valley up to the RSGH patio.
- 3 Jan 2012: Chris Roberts installed a new window fan.
Back to the top
Latest Pictures:
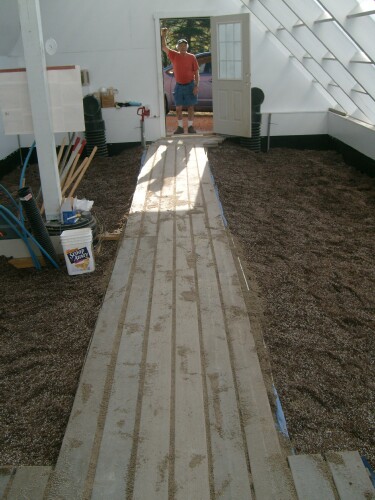
Walkway finished
|

Control box
|

Cistern installed |
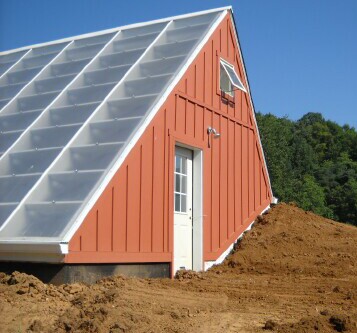
Backful done
|
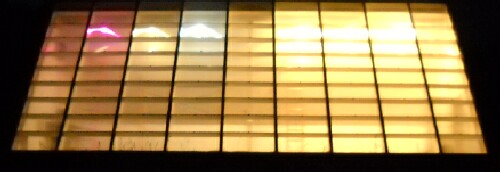
YSGH at night |
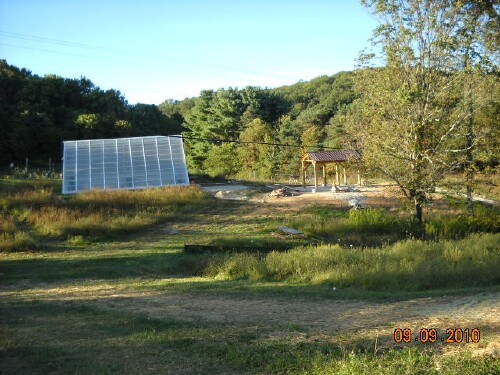 |
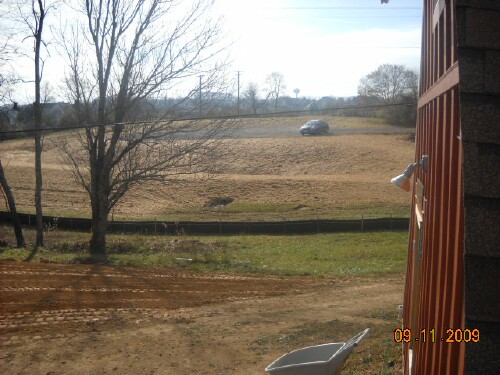 |
Energy being stored in the heat sink!:
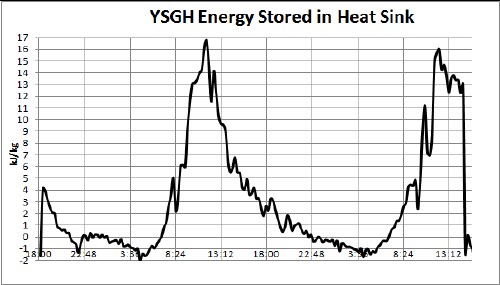 |
Snow:
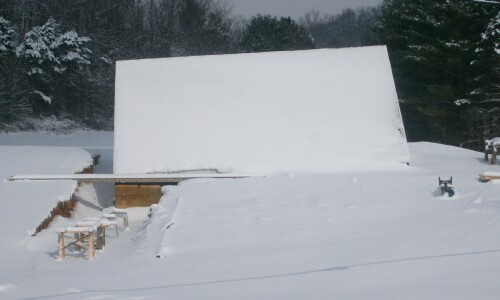 |
Back to the top
YMCA SGH Steering Committee
YMCA SGH Steering Committee consists of Tim Colley (architect), Pat Bixler (chair), Jason Boyle (Green Valley Builders, Inc.), Arlean Lambert (land owner), Dave Roper, Gail Billingsley (YMCA of VT), ), Justin Boyle (Green Valley Builders, Inc.), in the order left to right in the picture below.
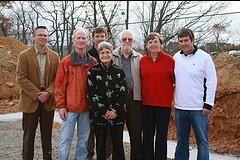
Contributors and Construction Companies
- L. David Roper: originator of concept for the YMCA SGH using SHCS, Steering Committee, donator of instrumentation and some building materials; much volunteer labor
- The Solar Greenhouse Book edited by James C. McCullagh, Rodale Press, 1978: SGH informatio
- SunnyJohn.com: SHCS first adopter in the United States for SGH
- Gail Billingsley (Executive Director of YMCA at Virginia Tech): VT YMCA involvement, Steering Committee
- Arlean Hale Lambert: land owner
- Colley Architects: architectural plans, Tim Colley, owner & YSGH Steering Committee
- Truesdell Engineering: structural analysis
- J. Patrick Bixler (owner of Baseline Solar Solutions; Executive Director of Sustainable Blacksburg): overall planning and direction, Steering Committee chair
- Dave Nickerson: physical model builder
- Anderson and Associates: site plan; Designer: Steve Somick
- Green Valley Builders: construction supervision [Jason & Justin Boyle], Steering Committee [Justin Boyle]
- Naraine Persaud: instrumentation planning and installation, later including a $27,000 grant for instrumentation.
- Abigail Convery (Associate Director of YMCA at Virginia Tech): VT YMCA volunteers & planters organizer
- J. W. B. Contractors (Jeff Buchinsky): excavation, cistern installer and backfill
- Conrock: concrete for footers and walls; footers installed by Green Valley Builders
- Reward Walls: ICF supplier, Tim Barnett (ICF made from recycled materials.)
- ICF installation: Jason Boyle, Justin Boyle, Doug Hoback, Tim Hoback, Dave Roper, Pat Bixler, B. Patrick Sisk (Bottom Creek Builders), Dustin Derrick (Evergreen Insulation), Matt Schmidt (PBS Contracting, Inc.), Patrick Feucht & Gail Billingsley.
- Concrete pump truck for walls: Jeff Ligon.h
- ICF waterproofing: Snyder & Associates.
- Battery backup for electrical system: Solar Connexion (Bryan Walsh).
- Electrical work: Chris Roberts (Baseline Solar Solutions)
- Aquarius plumbing (David Bernard) : pumped rain water off of the heat sink tarp.
- Photography: Bob Sisk.
- Sun Gro donated 75 bales of organic soil mix. John Ogburn donated 5 bales,
- Beam, rafters and end-framing installation: Richard Reid, Tom Bowden (Restorations Unlimited), Hammer Down Construction (John Sullivan, owner).
- Seanie White of Infinity Windows for vent windows from Marvin Windows.
- Closed-cell foam insulation: Evergreen Insulation (Dustin Derrick, owner), Travis Radford & Daniel Webber.
- Shingles donator and installer: Henderson Roofing (Tim Henderson).
- Hardie-board installer: DiStefano Siding Company, Moneta VA, Steven T. DeStefano, owner.
- The composite boards for the top of the walkway were donated by Green Valley Builders (Trex) and L. David Roper (ChoiceDek).
- Guttering installed by Blue Ridge Seamless Gutter.
- Landscaping grant from Master Gardeners.
- Vermiculture grant from Master Gardeners.
- Hale-YMCA Community Gardens parking lot and path to the YMCA Solar Greenhouse by UXB International using the Kimsroads technique.
- David King (King & Sons Excavating) put the water-pressure tank inside and put the sump pump in the cistern.
- Superior Exterminating Company did the termite treatment around the building.
Back to the top
Planting
For the remainder of the winter of 2008 the YSGH will be divided into two parts, separated by a north-south line through the center post. The east half will be planted and cared for by students of Blacksburg New School and the west half will be planted by a group of gardeners organized by John Ogburn and Deborah Wiley.
Data
Several data loggers are used to collect data for the YMCA Solar Greenhouse. Here are some data collected by a data logger placed on the south side of the center post.
Data for April 2009 before the heat-sink and the vent fans were installed:
|
Temperature and light intensity (right scale): 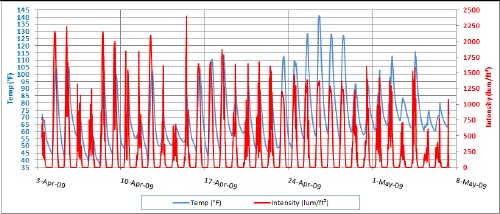
Note that temperature slightly lags light intensity. |
Look at temperature by itself: 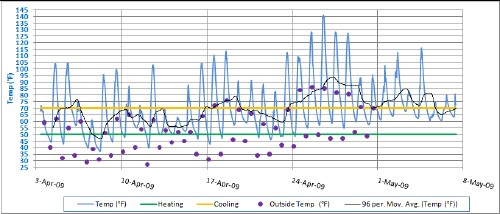
The black curve is the 2-day running mean. |
See YMCA Data web page for more information about data.
Solar greenhouses communications
Weather Stations in Blacksburg for Observing Micro-Weather
Roanoke Community Garden Association
Back to the top
L. David Roper, http://www.roperld.com/personal/roperldavid.htm; roperld@vt.edu
24-Jul-2019